With over two decades of experience, GEP has elevated logistics procurement for global enterprises, managing billions in spend across various industries and transport modes. Our comprehensive approach has not only led to significant savings and enhanced service levels but also strengthened supplier relationships and minimized risks. Recognizing the cyclical nature of transportation, GEP ensures competitive rates without compromising service, fostering long-term business health and sustainable carrier relations.
Expertise Drives Value
We classify key transportation lanes, identify "at risk" areas, and evaluate market and operational constraints like metro accessibility and back-haul opportunities. Our sourcing strategies, including supplier partnerships and carrier capacity management, are backed by network optimization, encompassing warehouse locations and transit times. Supported by our vast SME infrastructure, extensive supplier database, and advanced analytical and optimization tools, GEP consistently delivers 10-20% savings in logistics categories.
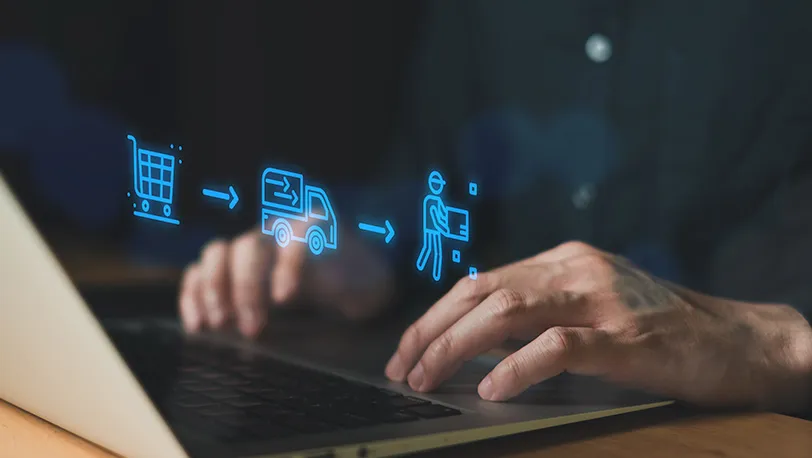
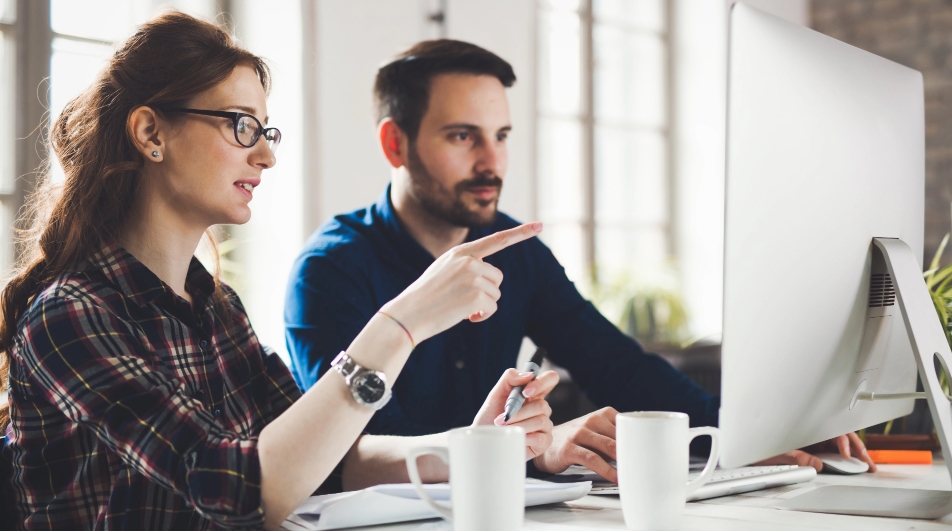
CATEGORY EXPERTISE
Frequently Asked Questions
Effective collaboration between procurement and logistics management requires deliberate alignment of processes, objectives, and information flows across these traditionally siloed functions. At the strategic level, integrated planning sessions ensure logistics considerations guide supplier selection decisions while procurement insights guide network design and transportation strategies.
Information sharing serves as the foundation for day-to-day collaboration. Leading organizations implement digital platforms that provide both functions with visibility into purchase orders, inbound shipments, inventory levels, and supplier performance. This shared visibility enables coordinated decision-making during supply disruptions or demand fluctuations.
Cross-functional teams that include both procurement and logistics professionals have proven particularly effective for strategic categories with complex logistics requirements. These teams develop integrated strategies that optimize total landed cost (that is, the comprehensive cost of a product) rather than focusing exclusively on purchase price or transportation expense.
Joint supplier management represents another critical collaboration point. While procurement typically leads supplier selection and contract negotiation, logistics teams participate in defining delivery requirements, compliance standards, and performance metrics. This collaborative approach ensures logistics considerations are addressed during supplier onboarding.
Regular performance reviews that examine both commercial and operational metrics foster continued alignment. These reviews should evaluate metrics such as on-time delivery, fill rate, and inventory turns along with traditional procurement metrics such as cost savings and contract compliance.
Organizations that excel in procurement-logistics collaboration typically establish formal coordination mechanisms while encouraging informal communication between these interdependent functions.
A procurement and logistics management expert serves as an integrator who bridges the commercial and operational aspects of supply chain management. This specialized role requires deep expertise in both disciplines, enabling holistic optimization of supply processes from source to consumption.
Strategic responsibilities include developing integrated category strategies that balance purchase cost against transportation expenses, inventory carrying costs, and supply risk factors. The expert conducts comprehensive total cost analyses that incorporate all logistics-related expenses into sourcing decisions, avoiding sub-optimization that occurs when procurement and logistics operate in isolation.
On the operational front, the expert orchestrates day-to-day coordination between purchasing and logistics teams, resolving conflicts between cost-efficiency and service-level objectives. This includes aligning inbound delivery schedules with production needs, warehouse capacity, and transportation constraints.
Supply base management represents another key responsibility. The expert develops supplier performance metrics that encompass both commercial terms and logistics capabilities, ensuring vendors are evaluated on their total contribution rather than price alone.
Technology enablement has become increasingly important, with experts identifying and implementing digital solutions that provide end-to-end visibility from purchase order to delivery. These systems facilitate collaborative planning and exception management across organizational boundaries.
In many organizations, the procurement and logistics management expert also leads change management initiatives that break down traditional functional silos, fostering a more integrated approach to supply management through shared objectives and aligned incentives.
Procurement logistics comprises several interconnected elements that together create an integrated approach to managing the flow of materials from suppliers to point of use.
Supplier network design represents the foundational element, determining the optimal geographic distribution of suppliers relative to manufacturing and distribution facilities. This includes decisions about supplier proximity, consolidation points, and regional vs. global sourcing strategies.
Inbound transportation management encompasses carrier selection, mode determination, route optimization, and freight terms negotiation. Advanced procurement logistics strategies include consolidated shipments across multiple suppliers and backhaul utilization to reduce transportation costs.
Inventory policy development balances material availability against working capital requirements. This includes establishing optimal order quantities, safety stock levels, and replenishment triggers based on lead time variability and demand patterns.
Receiving and quality inspection processes ensure purchased materials meet specifications upon arrival, with clearly defined protocols for handling non-compliance and supplier corrective actions.
Materials handling and internal logistics involve the efficient movement of received goods into production or storage locations, including warehouse slotting strategies and material presentation methods.
Performance measurement systems track key metrics across the procurement logistics process, including on-time delivery, order accuracy, lead time consistency, and total landed cost.
Information systems integration enables seamless data flow between procurement, logistics, and supplier systems, providing visibility throughout the order-to-delivery cycle and supporting collaborative planning and exception management.
Risk management strategies address potential disruptions through contingency planning, alternate sourcing arrangements, and buffer inventory at critical nodes.